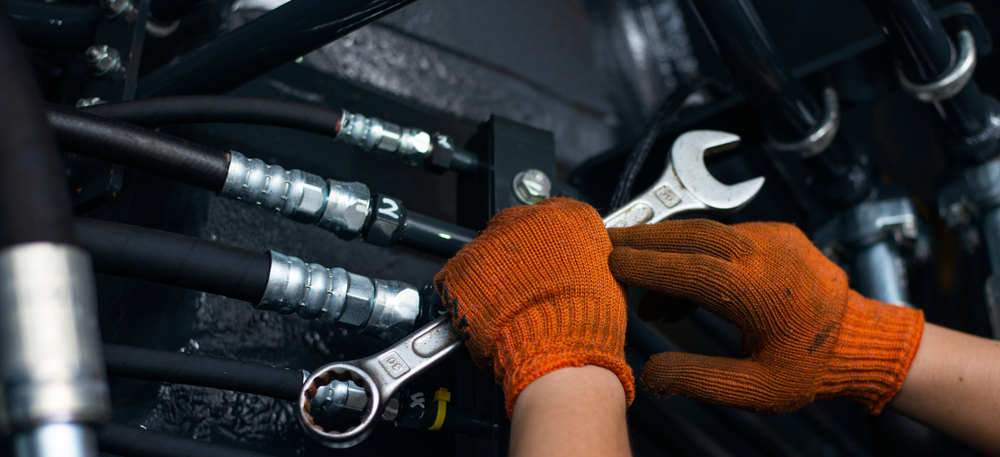
Hydraulic equipment is a cornerstone of many industrial and commercial applications, providing the muscle behind operations ranging from construction and manufacturing to aviation and marine engineering. Proper care and maintenance to extend the lifespan of your hydraulic equipment is essential for ensuring reliability, safety, and cost-efficiency.
This blog outlines the best practices for maintaining hydraulic equipment, helping you maximize its operational life while minimizing downtime and repair costs.
Understanding the Importance of Maintenance
Hydraulic systems operate under extreme pressure and high stress, making them susceptible to wear and tear. Regular maintenance not only prevents sudden failures but also improves efficiency and performance. Here are some compelling reasons why proper care and maintenance to extend the lifespan of your hydraulic equipment is vital:
- Cost Efficiency: Preventive maintenance reduces costly repairs and replacement expenses.
- Enhanced Safety: Well-maintained equipment minimizes the risk of accidents.
- Optimal Performance: Regular upkeep ensures the equipment operates at peak efficiency.
- Extended Lifespan: Proper care delays wear and tear, significantly prolonging equipment life.
Common Causes of Hydraulic Equipment Failure
To maintain hydraulic equipment effectively, it’s crucial to understand what causes failures. The most common issues include:
- Contaminated Hydraulic Fluid: Dirt, water, and other contaminants compromise fluid quality, leading to system inefficiencies.
- Overheating: High temperatures accelerate component wear and reduce fluid lifespan.
- Improper Usage: Overloading or using the equipment outside its design parameters causes stress and damage.
- Neglected Maintenance: Ignoring routine checks allows minor issues to escalate into significant problems.
By addressing these factors, you can proactively reduce the risk of equipment failure.
Key Maintenance Practices for Hydraulic Equipment
Routine Inspection and Monitoring
Regular inspections are fundamental to identifying and addressing potential issues before they escalate. Create a detailed checklist that includes:
- Visual Inspections: Look for leaks, cracks, or unusual wear on hoses, seals, and fittings.
- System Monitoring: Check pressure gauges, fluid levels, and temperature readings to ensure they are within recommended ranges.
- Noise Levels: Listen for unusual sounds, such as knocking or whining, which may indicate internal issues.
Fluid Maintenance
Hydraulic fluid is the lifeblood of any hydraulic system. Maintaining its quality and level is crucial:
- Regular Fluid Checks: Inspect fluid levels daily and top up as needed.
- Replace Contaminated Fluid: Use a high-quality filtration system to remove contaminants and replace old fluid regularly.
- Monitor Viscosity: Ensure the fluid’s viscosity matches the manufacturer’s specifications for optimal performance.
Hose and Seal Maintenance
Hoses and seals are critical components that often suffer from wear and tear due to high pressure and environmental factors:
- Inspect for Wear: Regularly check for cracks, abrasions, or bulges in hoses.
- Replace Aging Components: Swap out old hoses and seals to prevent leaks and failures.
- Use Compatible Materials: Ensure replacement parts are compatible with your equipment’s specifications.
Keep the System Clean
Contaminants are among the leading causes of hydraulic system failures. Maintaining cleanliness reduces the risk of contamination:
- Filter Maintenance: Replace filters regularly to keep contaminants out of the system.
- Clean Work Areas: Always work in clean environments to minimize the risk of debris entering the system.
- Protect Components: Use dust caps and plugs during repairs to prevent contamination.
Temperature Control
Overheating can severely damage hydraulic equipment. Maintain optimal temperatures by:
- Checking Cooling Systems: Ensure radiators and coolers are functioning correctly.
- Avoiding Overuse: Allow equipment to cool down after prolonged operation.
- Monitoring Temperature Gauges: Address any abnormal temperature increases immediately.
Building a Preventive Maintenance Schedule
A structured preventive maintenance schedule is the backbone of extending the lifespan of your hydraulic equipment. Here’s how to create one:
- Determine Maintenance Intervals: Base intervals on the manufacturer’s recommendations and your equipment’s operational intensity.
- Record Maintenance Activities: Keep a detailed log of all inspections, repairs, and replacements.
- Set Reminders: Use software or manual calendars to ensure timely maintenance.
- Involve Experts: Consult with technicians or manufacturers for guidance on best practices.
Training and Knowledge Sharing
Proper care and maintenance require a knowledgeable team. Invest in training your personnel to:
- Understand Hydraulic Systems: Teach them the basics of hydraulic equipment operation and maintenance.
- Recognize Warning Signs: Equip them to identify early signs of wear and tear.
- Perform Basic Maintenance: Empower them to handle minor repairs and adjustments.
Benefits of Professional Servicing
While regular maintenance can be performed in-house, periodic professional hydraulic servicing is invaluable:
- Expert Analysis: Professionals can identify issues that might be overlooked.
- Advanced Diagnostics: They use specialized tools to assess the system thoroughly.
- Warranty Compliance: Professional servicing ensures maintenance meets manufacturer requirements, preserving warranties.
Modern Tools for Maintenance Optimization
Leverage modern technologies to streamline maintenance efforts:
- IoT Sensors: Install sensors to monitor fluid levels, pressure, and temperature in real-time.
- Predictive Analytics: Use software to predict maintenance needs based on operational data.
- Automated Alerts: Set up alerts to notify you of deviations from normal operating conditions.
Conclusion
Hydraulic equipment is a significant investment, and ensuring its longevity through proper care and maintenance is both practical and cost-effective. By following the best practices outlined above, you can optimize performance, reduce downtime, and extend the lifespan of your hydraulic systems. Remember, consistent attention to detail and a proactive maintenance approach are the keys to reaping the full benefits of your hydraulic equipment for years to come.
Got Questions About Industrial Machinery? Let Us Help!
Hydraulic Power Sales, Inc. is local manufacture, distributor, and service provider of hydraulics equipment based in Cordova, California. Since 1985, we have been providing hydraulic repair services, hose assemblies, and sales to businesses throughout northern California. We manufacture hydraulic engine systems and hydraulic cylinders while supplying other hydraulic equipment. We want to be your one source for all of your hydraulic/pneumatic needs. Give us a call today!