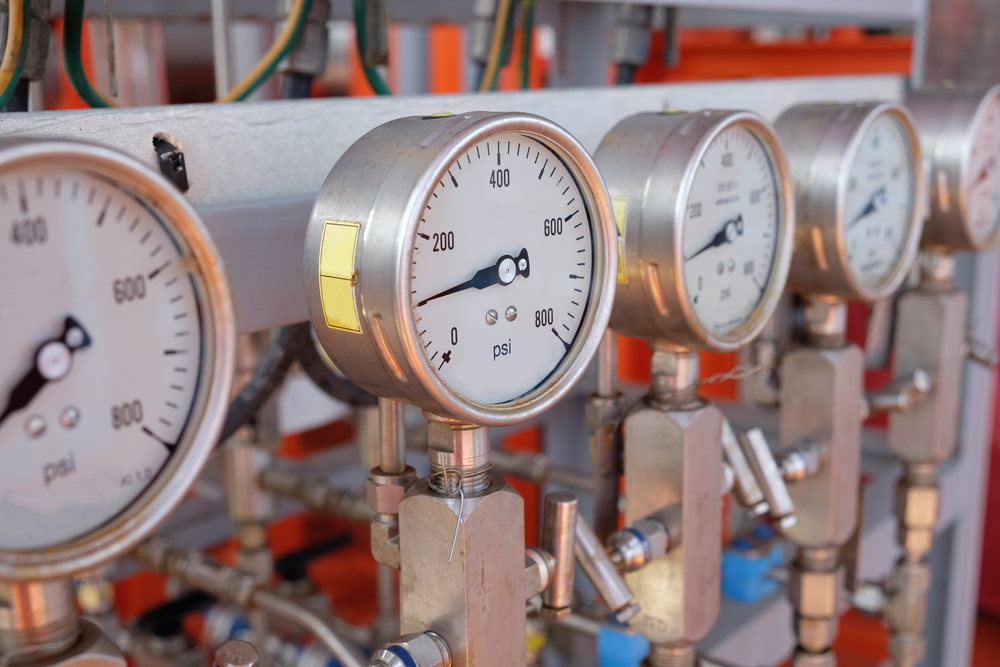
When it comes to choosing the right system for powering industrial equipment, businesses often find themselves weighing the options between hydraulic and pneumatic systems. Both types of systems have been widely used across industries for decades, each offering its own unique set of advantages. However, understanding the differences between hydraulic vs. pneumatic systems is crucial to making the right decision for your operation. In this blog, we’ll explore the core differences, benefits, and applications of each system, helping you decide which one best suits your needs.
The Basics of Hydraulic and Pneumatic Systems
To understand the differences between hydraulic vs. pneumatic systems, it’s important to first look at what each system entails. Both are classified as industrial fluid power systems, but the way they operate and the fluid medium they use are quite different.
Hydraulic systems rely on the use of liquids, typically oil, to transfer power. In these systems, a pump pressurizes the fluid and sends it through a network of pipes to actuate mechanical devices like cylinders or motors. The liquid’s incompressibility makes hydraulic systems highly effective for applications requiring heavy lifting, precise control, and significant force output.
On the other hand, pneumatic systems use compressed air as their power source. The air is pressurized by a compressor and is then directed through pipes to actuate components like cylinders and motors. Since air is compressible, pneumatic systems are generally best suited for applications where high-speed movement or lighter forces are needed. The inherent elasticity of air can also allow for more controlled, smoother motions.
Key Differences Between Hydraulic and Pneumatic Systems
One of the most significant differences between hydraulic vs. pneumatic systems lies in the medium they use to transmit power. As mentioned earlier, hydraulics rely on incompressible liquids like oil, while pneumatics depend on compressed air. This fundamental difference in the fluid used impacts many other aspects of each system, from performance to environmental considerations.
Hydraulic systems can provide much higher levels of force and precision. The incompressibility of the hydraulic fluid means that these systems can generate greater power output and are ideal for tasks like lifting heavy loads or moving large machinery. Hydraulic systems are commonly found in industries such as construction, automotive, and manufacturing, where such capabilities are needed. For example, hydraulic systems in Rancho Cordova are often used to power the heavy machinery at construction sites, providing the necessary force for lifting and excavation tasks.
Pneumatic systems, on the other hand, are generally lighter and less powerful. They are used in applications where speed, agility, and light lifting are the primary concerns. Pneumatic systems are commonly seen in packaging, food processing, and light manufacturing industries. Because compressed air is abundant and relatively inexpensive, pneumatic systems are often the go-to solution for tasks such as moving lightweight objects, operating conveyors, or packaging products. They are also favored in industries where environmental cleanliness is crucial, as compressed air is clean and doesn’t leave behind residues like oils or fluids.
Performance, Efficiency, and Maintenance
When comparing hydraulic vs. pneumatic systems, another important factor to consider is performance. Hydraulics offer superior performance in terms of force and precision. The high pressure at which hydraulic systems operate allows them to generate much more power than pneumatic systems. For instance, in hydraulic systems, pressure can reach up to 5,000 psi or more, enabling them to move extremely heavy objects. This makes them indispensable in industries where heavy lifting or precise movement is required, such as aerospace or heavy equipment manufacturing.
However, hydraulic systems do have some trade-offs in terms of efficiency. The high pressures involved mean that hydraulic systems require robust components and rigorous maintenance to ensure they function properly. Leaks in hydraulic lines, for instance, can lead to significant losses in both efficiency and performance. Additionally, hydraulic fluid itself requires proper management to avoid contamination, which can lead to costly repairs and downtime.
Pneumatic systems, in contrast, are less efficient when it comes to power generation. Because air is compressible, pneumatic systems typically operate at much lower pressures—often in the range of 100 to 200 psi. While this makes pneumatic systems suitable for lighter tasks, they cannot match the sheer force and precision of hydraulic systems. However, pneumatic systems are generally easier to maintain and more cost-effective. They do not require as much lubrication or the maintenance of fluids, making them simpler to manage in many industrial settings. Pneumatic systems are often the better choice in environments where cleanliness is essential or where minimal downtime and low-maintenance costs are a priority.
Environmental Impact and Safety Considerations
Another critical factor when choosing between hydraulic vs. pneumatic systems is their environmental impact and safety concerns. Hydraulic systems use oil or other fluids, which can pose environmental hazards if leaks or spills occur. For this reason, industries using hydraulic systems must invest in preventive measures such as spill containment, fluid management, and regular inspection of equipment. Additionally, hydraulic systems often require the use of additives or synthetic oils, which may have environmental implications if not disposed of properly.
Pneumatic systems, on the other hand, offer distinct environmental benefits. Since pneumatic systems use compressed air, there is no risk of hazardous spills or contamination, making them ideal for applications in clean environments like food processing or pharmaceuticals. Furthermore, compressed air is an abundant and inexpensive resource, which makes pneumatic systems less reliant on specific chemical fluids and oils. However, it’s worth noting that pneumatic systems still consume energy to compress air, and inefficiencies in the system can lead to wasted energy, contributing to environmental concerns.
In terms of safety, both hydraulic and pneumatic systems have their own sets of risks. Hydraulic systems operate under high pressure, and failures such as hose ruptures or seal leaks can be dangerous. Hydraulic fluid can also pose fire hazards in certain circumstances, especially when exposed to high temperatures. Pneumatic systems, while generally considered safer in terms of fluid-related hazards, can still present risks. The high-speed movements of pneumatic actuators, combined with the potential for sudden pressure releases, can result in accidents if proper safety precautions are not followed.
Choosing the Right System for Your Operation
The decision of hydraulic or pneumatic, which is better, depends on the specific needs of your operation. If your work involves heavy lifting, precise control, or high-pressure tasks, a hydraulic system will likely be the better choice. The high force output and fine control of hydraulic systems make them ideal for industries like construction, manufacturing, and heavy machinery.
Conversely, if your operation requires high-speed movement, light lifting, or is concerned with environmental cleanliness, a pneumatic system might be more appropriate. Pneumatic systems are perfect for packaging, assembly lines, and situations where compressed air can be easily sourced. Moreover, industries looking to minimize maintenance and operational costs might find pneumatic systems easier to handle due to their simpler mechanics and the abundance of compressed air.
Ultimately, choosing between hydraulic and pneumatic systems comes down to assessing your specific needs. Consider factors such as the weight of the loads being moved, the precision required, the cost of energy and maintenance, and the potential environmental impacts of each system. Both hydraulic and pneumatic systems have their own unique set of advantages, and the right choice for your operation will depend on the specific tasks at hand.
Conclusion
Understanding the core differences between hydraulic vs. pneumatic systems will help you determine which is the right fit for your operation. Whether you need the powerful force of hydraulic systems or the speed and efficiency of pneumatic ones, both types of industrial fluid power systems play vital roles across various industries. By considering the specific demands of your operation, you can make an informed decision that enhances both performance and efficiency.
Got Questions About Industrial Machinery? Let Us Help!
Hydraulic Power Sales, Inc. is local manufacture, distributor, and service provider of hydraulics equipment based in Cordova, California. Since 1985, we have been providing hydraulic repair services, hose assemblies, and sales to businesses throughout northern California. We manufacture hydraulic engine systems and hydraulic cylinders while supplying other hydraulic equipment. We want to be your one source for all of your hydraulic/pneumatic needs. Give us a call today!