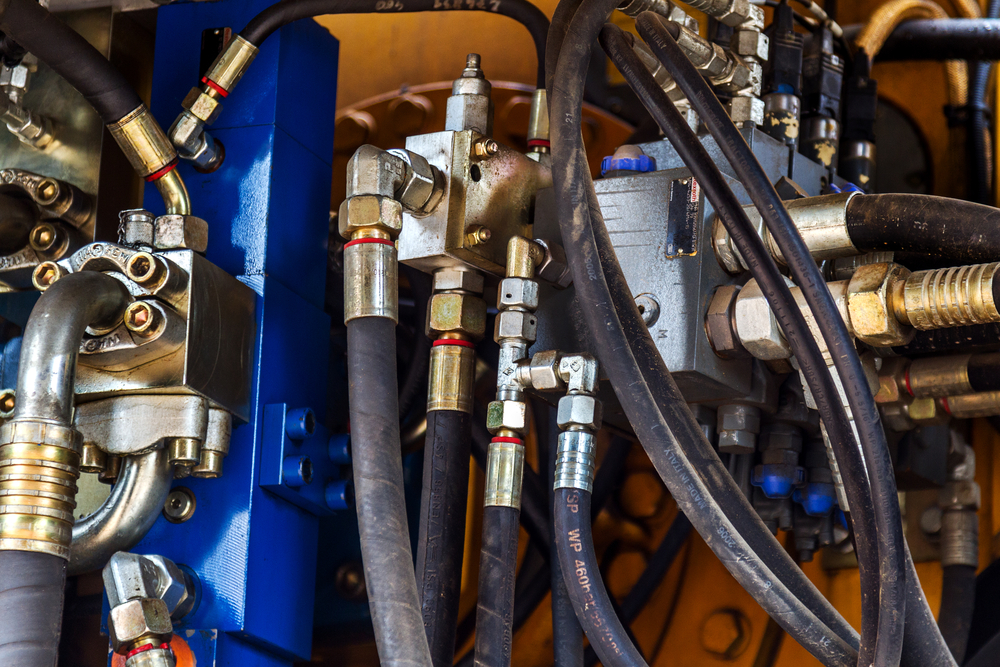
High pressure hydraulics technology has been a cornerstone of industrial applications for decades, enabling the efficient operation of machinery across various sectors, from manufacturing to construction. Recent advancements in this field have introduced groundbreaking methods and systems that are transforming the way industries approach hydraulics. These innovations promise not only to improve performance but also to reduce energy consumption and enhance safety standards. In this blog, we explore the latest developments in high pressure hydraulics technology and their implications for modern industries.
Emerging Materials Enhancing Durability and Efficiency
One of the most significant areas of innovation in high pressure hydraulics technology is the development of advanced materials. Traditional hydraulic systems often rely on steel and other durable metals, but these materials can be prone to wear and corrosion over time, particularly in high-pressure environments. The introduction of composite materials and high-strength alloys is revolutionizing the industry.
Composite materials, such as carbon fiber reinforced polymers, offer exceptional strength-to-weight ratios and improved resistance to corrosion. These materials are increasingly being used in hydraulic systems to reduce weight while maintaining structural integrity. Meanwhile, high-strength alloys, such as titanium and nickel-based materials, are being employed to withstand extreme pressures and temperatures, thereby increasing the lifespan of hydraulic components.
The adoption of these new materials is enabling manufacturers to design systems that are both more efficient and reliable. As a result, industries are experiencing reduced downtime and lower maintenance costs, which are critical for maintaining productivity.
Smart Sensors and IoT Integration in Hydraulic Systems
The integration of smart sensors and the Internet of Things (IoT) is another groundbreaking advancement in high pressure hydraulics technology. These innovations are allowing hydraulic systems to become more intelligent, providing real-time data on performance and system health.
Smart sensors embedded within hydraulic components can monitor variables such as pressure, temperature, flow rate, and fluid quality. This data is then transmitted to centralized systems or cloud platforms via IoT connectivity, enabling operators to analyze performance and identify potential issues before they escalate into costly failures.
Predictive maintenance is a key benefit of IoT integration. By analyzing data trends, operators can schedule maintenance proactively, avoiding unplanned downtime and extending the operational life of hydraulic systems. Moreover, these smart systems can optimize energy usage by adjusting hydraulic performance to match the specific demands of a task, contributing to overall energy efficiency.
The integration of IoT and smart sensors represents a significant leap forward, particularly for industries that rely on high pressure hydraulics technology in remote or hazardous environments. With enhanced monitoring and predictive capabilities, businesses can ensure the safety and reliability of their operations.
New Methods for High Pressure Hydraulics Technology Design
Innovations in design methodologies are playing a crucial role in advancing high pressure hydraulics technology. Engineers are leveraging cutting-edge simulation tools and computational modeling to create systems that deliver superior performance while minimizing risks.
Finite Element Analysis (FEA) and Computational Fluid Dynamics (CFD) are among the tools being used to simulate hydraulic system behavior under various conditions. These technologies enable engineers to predict how components will respond to extreme pressures and identify areas where improvements can be made. By optimizing designs before manufacturing, companies can save time and resources while ensuring the highest levels of performance and safety.
Another exciting development is the use of additive manufacturing, or 3D printing, to produce hydraulic components. This approach allows for the creation of complex geometries that are difficult or impossible to achieve with traditional manufacturing methods. Additive manufacturing also reduces material waste and shortens production times, making it a cost-effective option for developing high-performance hydraulic systems.
These new methods for high pressure hydraulics technology design are paving the way for systems that are more efficient, lightweight, and adaptable to a wide range of applications. As these approaches continue to evolve, they will likely become standard practice in the industry.
Enhanced Energy Efficiency and Sustainability
Energy efficiency and sustainability are becoming increasingly important in the development of high pressure hydraulics technology. Traditional hydraulic systems are often associated with high energy consumption, but new innovations are addressing this challenge through more efficient designs and sustainable practices.
One approach is the use of energy recovery systems. These systems capture and reuse energy that would otherwise be wasted, such as the energy generated during deceleration or pressure relief. By integrating energy recovery mechanisms, hydraulic systems can reduce their overall energy consumption and improve operational efficiency.
Another area of focus is the development of environmentally friendly hydraulic fluids. Traditional fluids can have a significant environmental impact if not properly managed. To address this, manufacturers are creating biodegradable and non-toxic alternatives that perform well under high-pressure conditions. These fluids help reduce the ecological footprint of hydraulic systems while maintaining their effectiveness.
Additionally, variable displacement pumps and energy-efficient actuators are being designed to optimize power usage. These components adjust their performance based on the specific needs of an application, ensuring that energy is not wasted. By incorporating these advancements, industries can achieve significant cost savings while contributing to global sustainability efforts.
The Future of High Pressure Hydraulics Technology
As we look to the future, the potential of high pressure hydraulics technology is vast. Ongoing research and development efforts are likely to yield even more innovative solutions that address the challenges faced by modern industries.
One promising area of exploration is the integration of artificial intelligence (AI) and machine learning into hydraulic systems. AI algorithms can analyze data from smart sensors to optimize system performance in real time, learning from past operations to improve efficiency and reliability. Machine learning models can also enhance predictive maintenance by identifying patterns that human operators might overlook.
Another exciting frontier is the use of advanced robotics and automation in conjunction with high pressure hydraulics technology. Robotic systems powered by hydraulics are already being used in applications such as construction, manufacturing, and medical devices. With further advancements, these systems could become even more versatile, capable of performing complex tasks with precision and speed.
Finally, the exploration of alternative energy sources, such as hydrogen-powered hydraulics, could revolutionize the industry. Hydrogen offers the potential for clean, high-energy-density power, making it an attractive option for applications that demand both efficiency and sustainability. While still in the early stages of development, this technology could play a significant role in the future of high pressure hydraulics.
Conclusion
The latest innovations in high pressure hydraulics technology are transforming the industry, offering new methods for design, improved materials, and enhanced energy efficiency. By embracing these advancements, businesses can achieve greater productivity, sustainability, and safety in their operations. As the field continues to evolve, we can expect even more groundbreaking developments that push the boundaries of what is possible with high pressure hydraulics technology.
Got Questions About Industrial Machinery? Let Us Help!
Hydraulic Power Sales, Inc. is local manufacture, distributor, and service provider of hydraulics equipment based in Cordova, California. Since 1985, we have been providing hydraulic repair services, hose assemblies, and sales to businesses throughout northern California. We manufacture hydraulic engine systems and hydraulic cylinders while supplying other hydraulic equipment. We want to be your one source for all of your hydraulic/pneumatic needs. Give us a call today!